Industry 4.0 is more than data and tools. It is a culture.
Industry 4.0- a term circulating in the industry for the last few years where companies say they are trying to adopt I4.0 practices into their manufacturing operations but have no idea what it truly means. There are a lot of divisions within the buzzword that include digitization, 3D printing, AI, augmented reality, IoT, digital twins, machine vision, and so on. For most companies, digitization or digital factory appeals the most, and it is considered one of the core aspects of Industry 4.0. One of the major misconceptions is the perception that digitization is the tool that enables it. The implementation of this would solve most problems that plague manufacturers. The misconception is false, and this perception hinders companies from taking the leap toward the next industrial revolution and becoming better versions of themselves. Even with the tools at their disposal, companies are not willing to change how they are working and use the tools in the right way to learn more about the issues they have and find solutions for them in a streamlined process.
The Industry 4.0 implementation mistakes
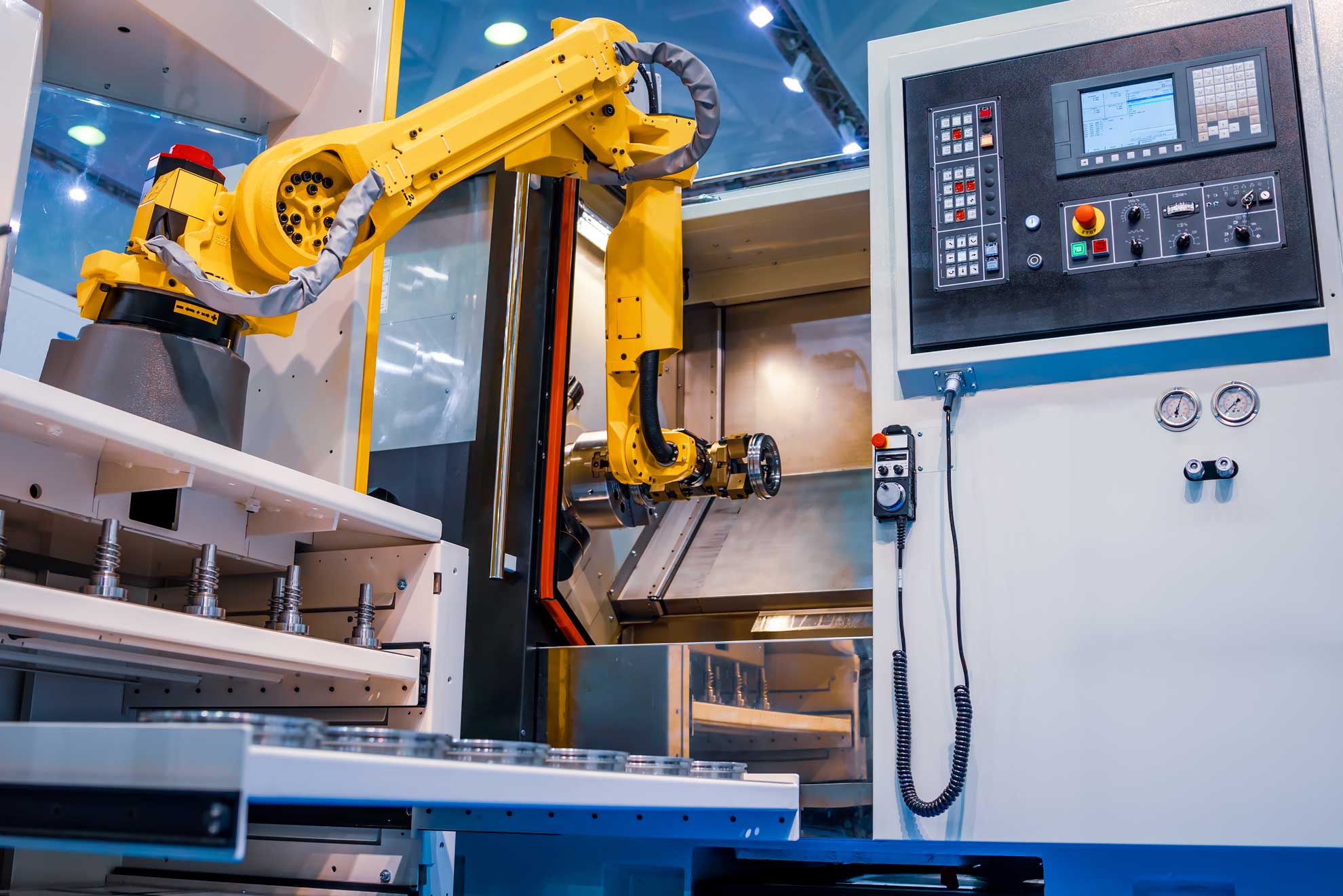
1. The focus is on the tools used rather than the goals they want to achieve using the tools
Digitization enables data traceability for the operations of a manufacturing enterprise. The issue with digitization is that most leaders within the sector invest in complex and sophisticated equipment to implement it without understanding why they are doing it and what problems it would solve. The implementation costs them money, effort, and time without helping them achieve the desired results. Focussing on the goals that they want to achieve and creating smaller pilot projects to achieve those goals would be a better way to solve the issues.
2. Leaders make shopfloor decisions without involving the shopfloor personnel
One of the issues within manufacturing organizations is that the shopfloor operational decisions lie with the upper management. Most of the time, the upper management is detached from the daily operational activities on the shop floor and does not know the actual problems. They make decisions based on perceptions rather than facts. This strategy means that when they invest in complex tools to solve the perceived problems, however good the tools may be, the shopfloor personnel will not use them. While companies should be open to change, the changes should be fact-driven, and issues that arise on the shop floor and decision-making in terms of what problems to solve should be taken collectively with input from the people working on the shop floor. In addition, the changes should be rolled out in a step-by-step and easy way to enable smooth adoption and track progress continuously.
3. Thinking that investing in the right tools will solve all the problems
Being just an Industry 4.0 adopter will not solve all the problems on the shop floor. Companies think buying the right tools to enable digital transformation will solve all their problems. The solutions available are one part, but the users need to use the tools effectively and see how it would be beneficial to solve the problems on the shop floor. Trying to solve all issues is also a mistake that manufacturers make, leaving them overwhelmed by the amount of information and possibilities that the sophisticated digital transformation tools provide that they do not know where to start. A step-by-step structured way of solving the problems using pilot tests can help focus on incremental improvements that add up to reduce and take control of the issues in the long run.
4. Untapped knowledge on the shopfloor
Most of the tools used to implement digitization, and help visualize the operations on the shop floor, do not use the knowledge available from the shop floor personnel. It could be by adding information about critical events happening on the shop floor that is different from the data collected. The knowledge and information can help improve the data quality and create a better system for implementing AI predictions. The AI predictions currently available falter as the data quality is ill observed and not vetted. The additional information from experienced personnel can help improve the quality of the AI engine within manufacturing.
5. Relying on gut feeling rather than on the data to make decisions
Manufacturers rely on gut feeling rather than on the data to make decisions. The situation continues after investing in the right tools to enable digitization and data traceability. While relying only on the data could also be detrimental, a combination of the data, additional information on the shop floor, and the knowledge of the personnel will help manufacturers flourish in the age of digitization.
Conclusion
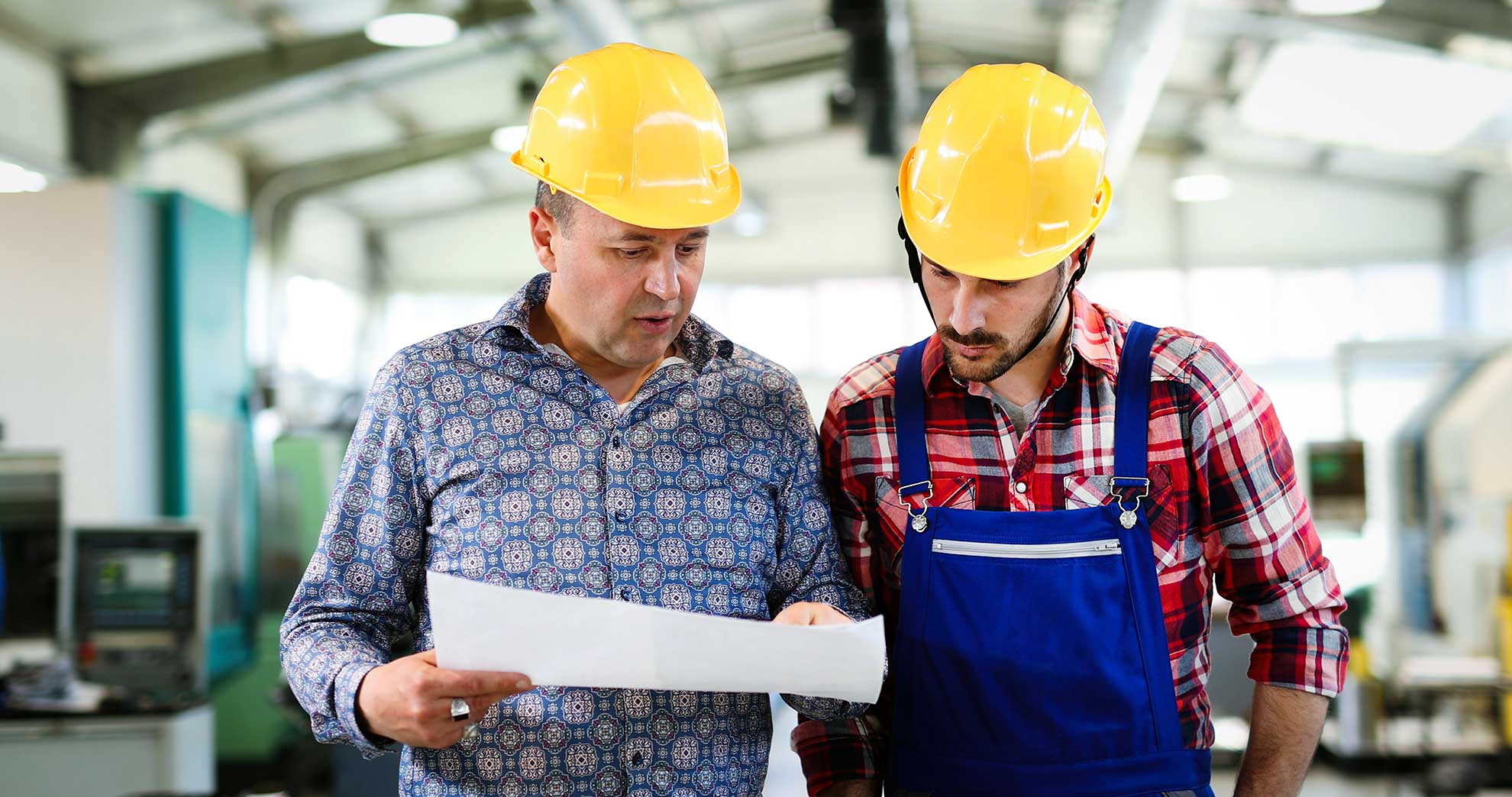
While it is good to see that manufacturers are trying to adopt Industry 4.0 and digitization tools, it is important to set specific goals that they want to achieve before focusing on the available tools. Sometimes complex tools are not required to solve the most pressing issues, so it is always better to focus on the problems rather than look for solutions. In addition, it is also important that decision-making rests with the people that experience the issues, so they can have a say on what tools they would like and what they would be most comfortable with before making any investment decisions. Focussing on simple solutions to solve daily problems can help ensure a smooth cultural transformation toward the next industrial revolution.