Four ways to gather machine data to improve your manufacturing productivity
Our goal is to help manufacturing companies become data-driven in their decision-making, using simple and readily available technologies. We realize that companies look for several factors when they look at data-collection and visualization solutions, and we have made our data-collection practices flexible enough to accommodate all these factors. We have non-invasive modes of data collection, and we also have solutions that gather data from the PLCs of the machines. Depending on the use case and the extent to which the companies use the data, we can suggest the best strategy for them.
Non-invasive sensors
SetApp
The SetApp is the easiest way to collect data regarding the utilization of a machine. Using our Android smartphone app that uses machine vision technology, we can gather data regarding a machine’s operation statuses like running, waiting, stopped, and off. The SetApp is a non-invasive way of collecting data. The SetApp looks at the Andon/stack light and sends a timestamp when there is a status change. The data collected allows plotting simple visual graphs to help managers and operators make data-driven decisions. The SetApp takes only a few minutes to get started, and it is the easiest way for companies to take the first step to become data-driven in their decision-making.
CT Sensor
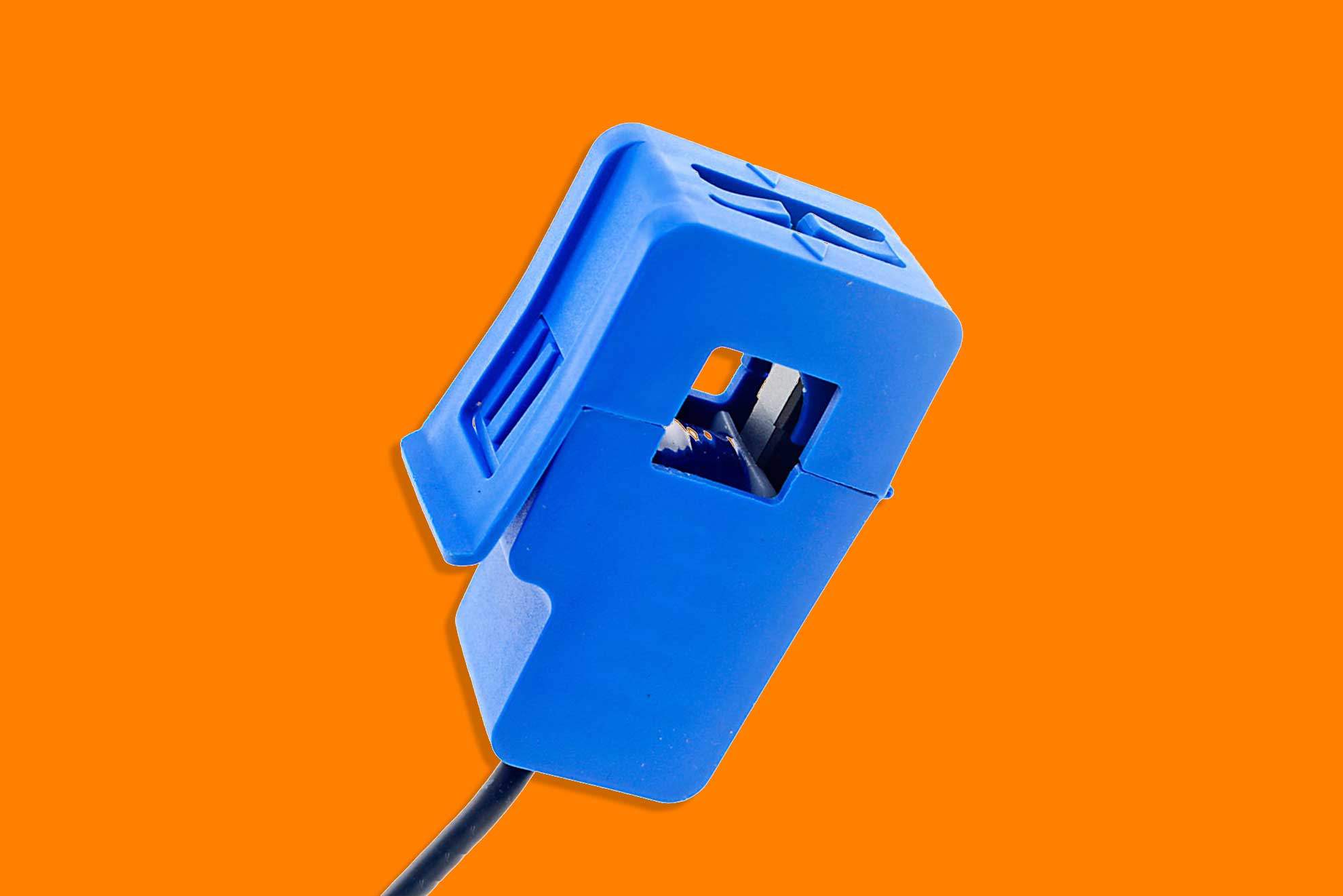
A CT sensor measures the alternating current consumption on a machine and, based on that, provides an idea about machine utilization. The sensor clamps around a current-carrying wire, and whenever the machine runs, the high current triggers a reading on the sensor that is accurate and reliable to know the state of the machine. The sensor couples to our edge device, the All Platform SetApp, where the data is processed and visualized. These sensors can monitor any machine or electrical equipment, and the installation is simple.
Industry protocols
MTConnect and OPCUA
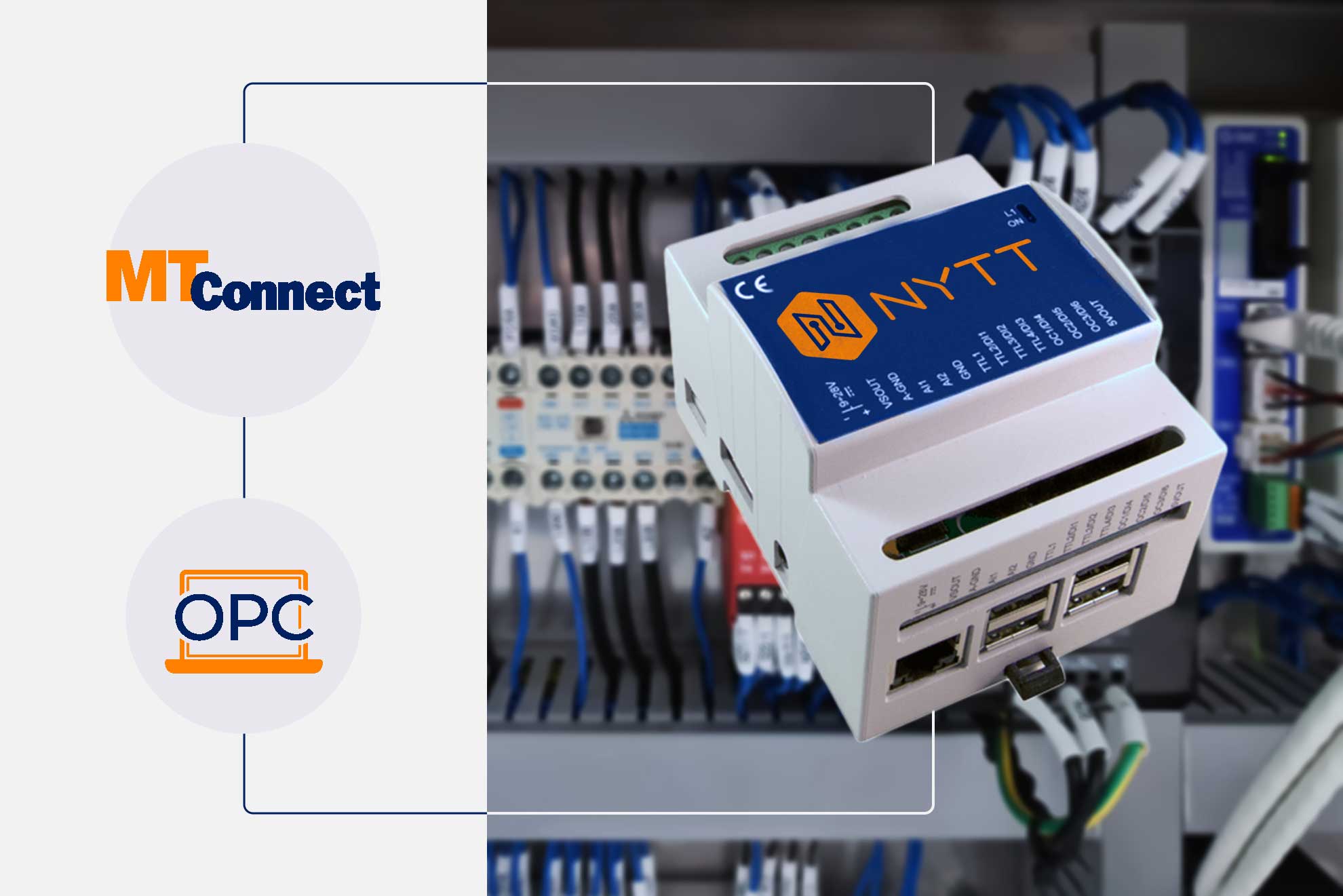
MTConnect and OPCUA are standard industry protocols that help to gather extensive data from the machines in a manufacturing facility. The licenses to these protocols might be expensive, but the data available include operational parameters like cutting speed, tool position, the tool used, machine failure reasons, and program codes. The abundance of data helps to find patterns in the operational parameters of the machines and predict when a machine failure might occur. The availability of failure codes means that the operators do not need to provide reasons, as it is collected directly from the controllers. Information regarding part information and cycle time of the parts means that calculations like OEE could be automated to an extent, making it an attractive option for companies that want to do extensive data analysis on their machines.
IO Signals
Digital signals from the machines in the form of ‘1’ and ‘0’ can be collected and analyzed easily using our All Platform Setapp. The binary data can provide important information on machine statuses or if a part is produced or not. The signal data is directly obtained from the machine PLCs and provide accurate information regarding the working of the machines.