Old equipment productivity increased by 7% using smart sensors
Background: the saw machine
The saw is the first machine in a series production which cuts parts for all the machines within the factory. The machine is utilised for long periods at a stretch and stays idle after stock replenishment. If the saw breaks down in the middle of preparation, it affects the working of the machines that follow.
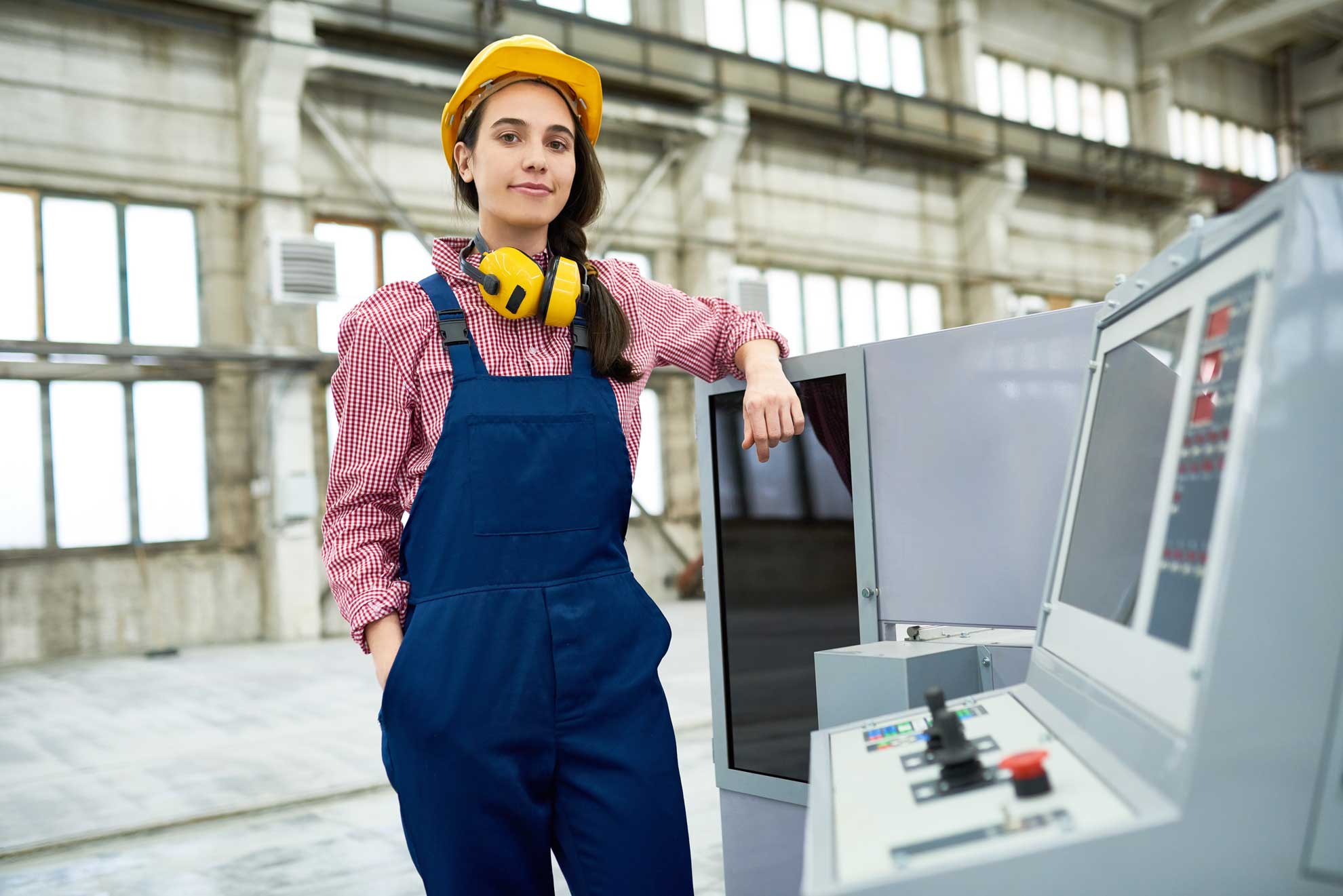
Problem and implementation
The manager needed to know the utilization levels of the saw machine but since it is a piece of old equipment, it did not have any sensors or protocols to understand how much it was working. Using non-invasive sensors connected to our APS, we could easily understand when the saw was working, waiting and stopped, giving the manager a clear picture of its utilization.
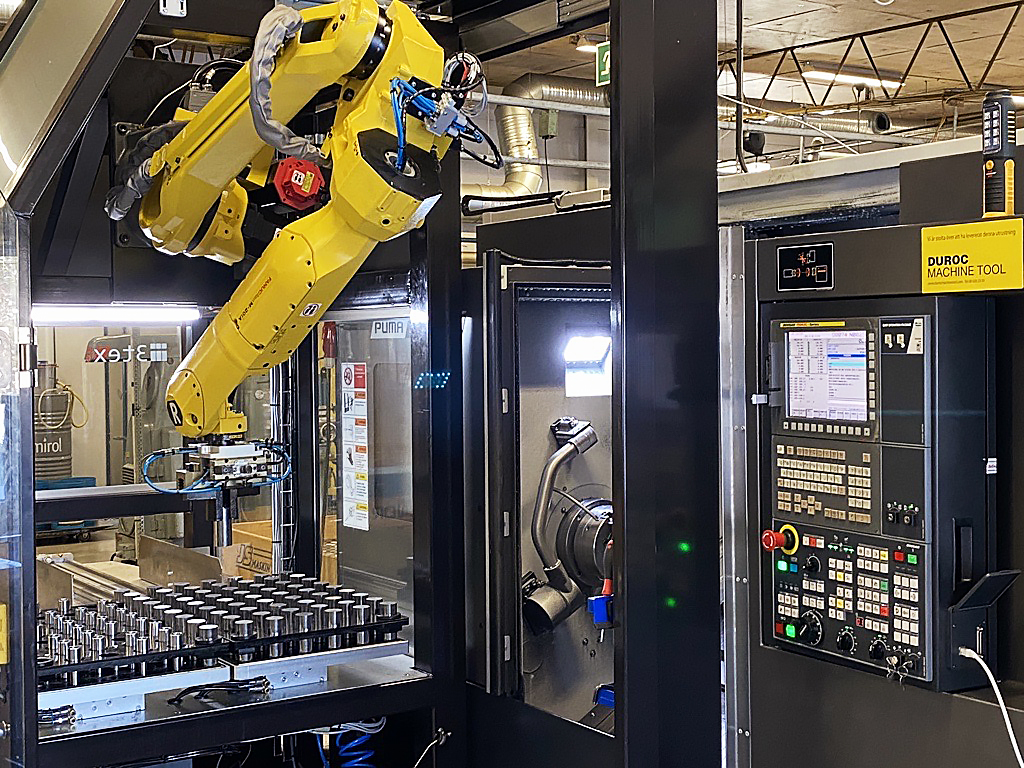
Results
The data collected showed that the stoppages of the saw coincided with lunch breaks, meeting times, and shift changes. These stoppages were due to planning issues missed by the ERP system. Using the data collected, we helped the manager fill up these gaps by creating a better planning schedule to make sure these stoppages do not occur.This resulted into following gains:
• 40 hours of production saved per month • 7,5% increase in utilization • 400more parts added to stock • 40k SEK of profit added in a month
This shows the power of shop-floor and data driven decisionsand the potential of the Nytt system!